KG2530 4 or 6 Axis-Hob Sharpening Machine
Extremely Accurate Multiple Machining Processes in a Single Part Chucking for High Precision Parts
・ Hydraulic / Pneumatic Precision Parts
・ Optical Machinery Parts
・ Electrical Machinery Parts
・ Aerospace Parts
KY20 Machining Process of Scroll
・ Machining of Scroll
・ Machining of Reference Pin Hole
・ Turning of End Faces
・ Machining of Seal Grooves
・ Tapping
・ Machining of Key Ways/Chamfering
・ Lathing of Heat Treated Shaft Area
Kashifuji's expertise with many years of hobber manufacturing is put to use in the precise positioning of the part spindle head slide as well as the high-speed part spindle. The part spindle utilizes ultra high precision angular contact ball bearings. Also, special care is taken with dynamic balancing during assembly. The part spindle (C-axis) incorporates a high precision optical scale providing highly accurate indexing.
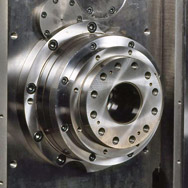
The machine bed utilizes a tilted rib construction for maximum rigidity. The V-shaped narrow guideways increase motion performance, and provide micron machining accuracies for many years.
Additionally, the column is symmetrical in design to the part spindle head slide for high thermal stability.
The tool spindles utilize ultra high precision angular contact ball bearings. Various types of tool spindles such as the belt driven, provide 6,000~18,000 RPM or the built-in motor style producing 30,000~75,000 RPM are available. These spindles deliver superb accuracies within 1μm of runout as well as low vibration.
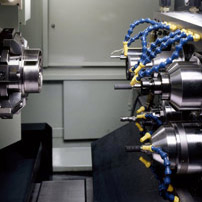
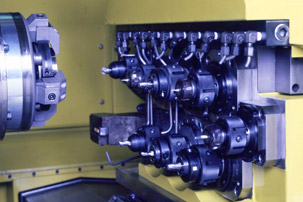
With the matrix tooling system, tool spindles can be incorporated in the machine for maximum productivity. No mounting errors related to tool change-over in the matrix tooling system allow highly accurate machining. Also, movement from tool to tool is extremely fast resulting reduced non milling time.
The machine movement from tool to tool is done by a short range positioning. Rapid infeeds are unnecessary, and unreasonable acceleration/deceleration is not required. As the ATC is not utilized, intermittent tool spindle rotation from 0 to ten thousands level RPM is not required. Also, an energy saving type (2.2~7.5 kW) spindle motor can reduce the factory electric power consumption.