KE201/251 6 Axis-CNC Hobbing Machine
A Warm-Up Free and Complete Dry Cut Hobbing Machine (Wet Cut Hobbing Machine or Wet/Dry Cut Hobbing Machine is optionally available.)
- Features
- Vertical Hob Machine
- Zero backlash Table
- Hand sclaped guidways
- Hard hobbing
- Programming
- Autmation
・ Large Automotive Transmission Gear
・ Truck Gear
・ Final Ring Gear
・ Motorcycle Gear
・ Agricultural Machine Gear
・ Construction Machine Middle Size Gear
KE201/251 Dry Cut Hobbing
KE201/251 Wet Cut Hobbing (Water Soluble Coolant)
The X, Y and Z axes guideways are hand-scraped to increase the way load bearing capacity which creates stable hobbing of large module gears. The machine body has a flat and narrow design by optimally allocating the peripheral equipment into mechanical free areas. Also, the design of the covers, wiring and piping around the hob head is significantly improved creating a “clean” machine appearance.
There are two types of machine footprints available depending on the factory layout. One is type A (standard) which has a narrower machine width than its predecessor. The other is type B which is suitable for an automated part transfer production line.
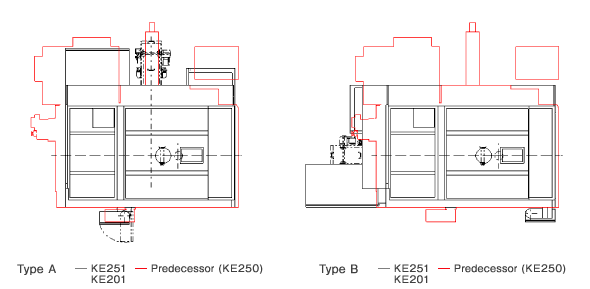
The newly developed “Tooth Thickness Stabilizer” Compensation Device maintains the center distance between the hob/work table and is included as a standard feature. Due to this “Tooth Thickness Stabilizer” the KE201/251 delivers a stable O.B.D. (tooth thickness) size producing a variation of less than ±10 μm from mean size.
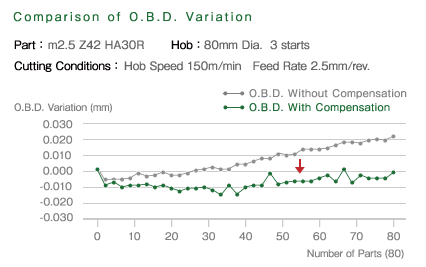
Ultra-fast dry cut hobbing at a surface speed of 300m/min is possible. Also, large pitch gears, which are difficult to dry cut, can be hobbed with the use of water soluble coolant allowing high speed hobbing as fast as dry cut hobbing (Optional modifications to the machine are required when using water soluble coolant).
The new lubrication system using low-viscosity grease is employed. With this system the lubrication cycle interval is extended as compared to the previous oil circulating system providing a significant reduction of lubrication oil consumption.
By utilizing a 4 station ring loader, chamfering and deburring can be performed during the hobbing cycle. Efficient use of machine’s open tooling area and independently aligned chamfer and deburring axes allow for easy adjustments / changeovers from the front of the machine. Additionally, the production line length & cycle time are reduced due to the combined operations of hobbing, chamfering and deburring.