KN152 6 Axis-CNC Hobbing Machine
Ideally suited for Hobbing Long Shaft Parts Dry/Wet Cut Hobbing as Standard Specifications (Wet Cut Hobbing Machine or Dry Cut Hobbing Machine is optionally available.)
- Features
- Vertical Hob Machine
- Zero backlash Table
- Hand sclaped guidways
- Hard hobbing
- Programming
- Autmation
・ Long Shaft Gear
・ Automotive Transmission Gear
・ Geared Motor
・ Compact Reduction Gear
・ Motorcycle Gear
・ Agricultural Machine Gear
KN152 Dry Cut Hobbing
Perfect for hobbing long shaft parts or, shafts with multiple splines/gears. The KN152 has 400 mm of Z axis (axial) stroke, longest for this size of hobbing machine in the industry, and 645 mm of distance from table top to tailstock center.
Also, Hard Hobbing, (finish hobbing process for hardened gears) produces a highly accurate tooth form, an overall increase in gear quality, at a low cost when compared to the grinding process it can replace.
The integrated column and tailstock column increases the thermal stability and minimizes the O.B.D. (size) variation from a cold start due to thermal deformation allowing for superb machining accuracies.
Additionally, the tooling area is wide open, making the operator’s accessibility to the hob cutter and jig fixture quite convenient. A part transfer unit such as auto part loader can easily be installed in this area while still allowing a compact machine foot print.
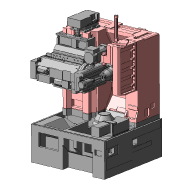
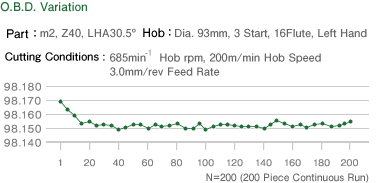
The KN152 was specifically developed as a complete dry cut hobber. The machine has increased slanted sections around the bed and column, and the hob saddle is protected by exit chute covers with few horizontal sections allowing rapid chip removal from the cutting tool area. Also, the new “Hanging” Style auto loader aids in an efficient and smooth chip removal.
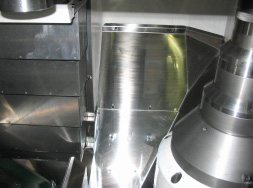
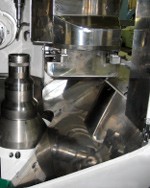
A new highly accurate hob head utilizing a built-in spindle motor and/or a highly accurate work table design with a built-in servo motor is optionally available for extremely accurate and high speed hobbing of small module gears. The high speed direct drive motor system of the hob head and work table delivers highly accurate finish hobbing equivalent to gear grinding or hard hobbing.
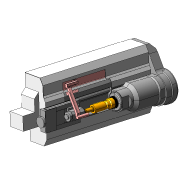
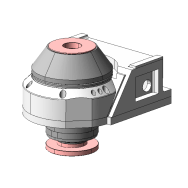
Chamfering and deburring can be handled in the tooling area of the KN152, after the completion of the hobbing cycle by using the Rotary Chamfering Device. Additionally, secondary burrs generated during the deburring phase, can be removed by rehobbing. “Hardened” secondary burrs remaining on tooth flanks which can remain after heat treat, can damage the grinding wheel used in finishing processes such as gear grinding and/or honing. Elimination of secondary burrs increases grinding wheel life. The production line length can be reduced due to the combined operations of hobbing, chamfering and deburring. The KN152’s Rotary Chamfering Device can also accommodate Shaft Gears.